
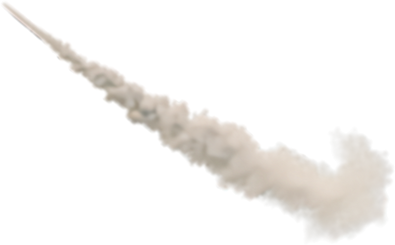
WE ARE

INNOVATIONS
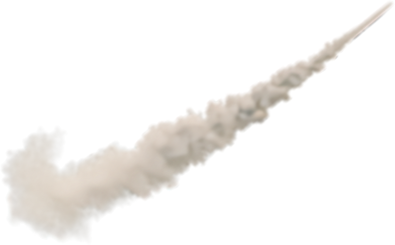
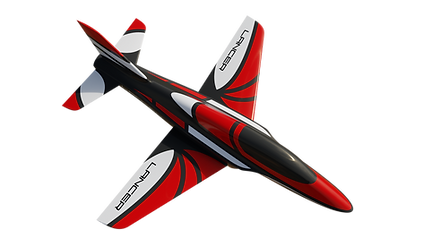

HOW WE MAKE OUR JETS
At FTL all of our planes are manufactured using very meticulous and stringent processes, ensuring the final result is of the highest quality and finish. Each of our jets are moulded using a one step moulding process to ensure they are kept as light as possible. We design and manufacture our own moulds which we believe are the best quality on the market.
Step 1 - The Design Phase
Each of our models is designed in house by our own expert. At this stage great attention is given to the small details that make our jets unmatched in design, weight and flight profile. We have decades of experience in this field and we only deliver the best quality in all of our models.
Step 2 - Moulding
Each jet is moulded in fibreglass using our own one step process and left to cure while it sets. During this process any additional glue is removed from the mould ensuring that the model is as light as it possibly can be and every effort is made to ensure that the moulding process will be successful and free of imperfections.
Step 3 - Internals
Once removed from the curing room the parts are inspected and then any required inserts are glued in place with a mixture of epoxy resin. These are carefully checked and positioned to ensure that they will fit perfectly once cured. Once the parts have set they are clamped into place with the corresponding face and left to set.
Step 4 Sanding & test fitting
Once remove from the moulds all surfaces are checked for imperfections and sanded / fitted with any other parts required. Finally they are test assembled to ensure all parts fit correctly and the tolerances to each part are correct for a perfect fit.
Step 5 - Undercoat
After the parts have received an initial test fit to ensure that they are good to go the parts are painted individually in our first paint room where they are are given a thorough coat and left to fully dry before moving on to the next stage in the process.
Step 6 - Pre-drilling for electronics
When they have dried the pieces are then prepared and cut where required for fitting purposes. Each piece is painstakingly sanded and test fitted for perfect fitment when the customer receives them. These are then passed upstairs for final preparation, filling and sanding where they will start to receive their final paint job.
Step 7 - Final surface preparation
Prior to starting the final paint application all of the surfaces are checked for imperfections filled and sanded fully to ensure the smoothest surface and most professional finish possible. A great deal of care is taken to ensure that each part has the very best finish possible prior to paint work being started.
Step 8 - Final paint layers
During the final painting stage the layers of paint are built up according to the design of the jet. Each phase is fully left to dry prior to another application of paint being applied. The end result is a very high quality model that has had every effort to ensure that is leaves us in immaculate condition.
Step 9 - The finished product
We take great pride in our hand made jets and we believe that they are some of the best on the market. The finish article will speak for itself both in the level of its finish and the flight characteristics it posses. We are flight enthusiasts ourselves and are passionate about the hobby. Each of our designs has been tested by pilots throughout the world